Learn about magpie swooping season in Victoria, from when it starts to who's at risk and easy ways to reduce you chance of being swooped this spring.
Australian car parts makers find a niche
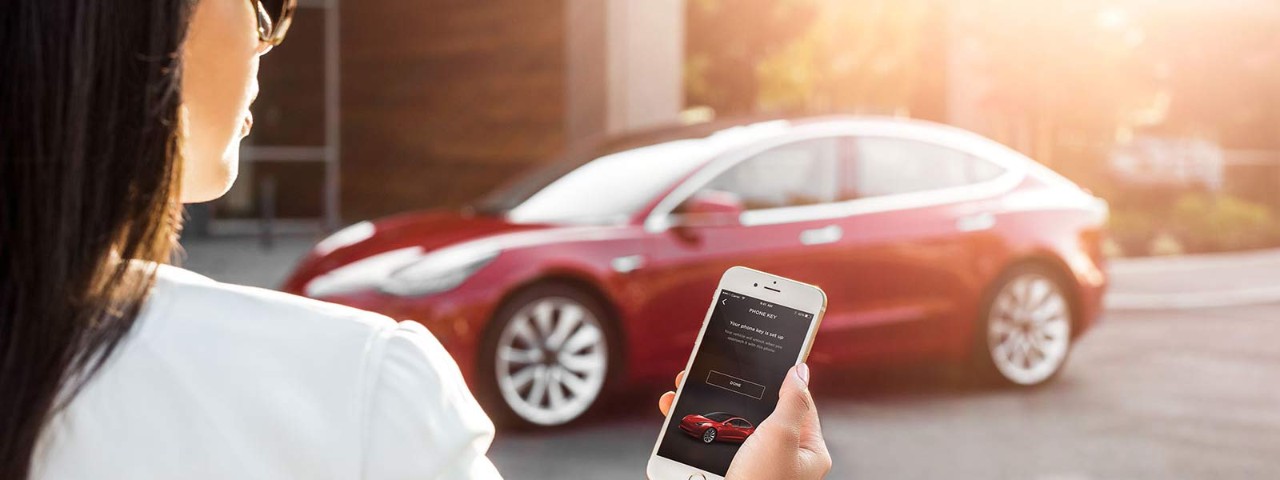
Local car manufacturing is dying, but niche players are carving out a high-tech market.
Australia will set a world first later this year when it becomes the first country to deliberately shut down its car manufacturing industry. It’s not a record that will be celebrated by many Australians.
The decisions by General Motors and Toyota to close their local assembly plants, following on from Ford’s shutdown late last year, will end a fabulous partnership between the country and a fully fledged automotive industry that really kicked off in 1948, although Australia had made its first cars in the late 19th century.
Over the past seven decades, the car industry became woven into Australia’s social fabric. It rode the economic boom of the 1950s and 1960s, giving employment to many thousands of migrants, allowing them to buy their own houses and cars and generally contribute to the country’s prosperity.
For a while in the 1950s, Holden was more profitable than its steel supplier BHP, and these rich pickings – which flowered behind a generous tariff regime – attracted the likes of Ford, Toyota, British Motor Corporation, Volkswagen, Chrysler, Nissan and Mitsubishi into Australian production.
Sum of its parts
While the car makers had a workforce of tens of thousands, they all relied heavily on a network of parts suppliers that employed several times that many people. While some of the largest parts suppliers were foreign companies that had followed their car-making customers – Bosch followed Volkswagen in the 1950s, for instance, and BorgWarner established itself alongside Ford in the 1960s – the vast majority of parts makers were Australian-owned.
Much-needed rationalisation led to the Button plan in 1986 and a steady reduction in tariffs that thinned out the ranks of not only the car makers but also parts manufacturers as the car companies gradually turned to cheaper offshore suppliers.
Of the remaining 150 parts makers in the Australian automotive industry, only 50 are expected to survive past 2017, through either founding offshore factories or diversifying into other products.
High-tech players
One interesting development in the past 10 years has a new, albeit small, wave of parts makers finding their own way in the world. Companies such as Carbon Revolution (wheels), Quickstep Technologies (lightweight panels) and Tritium (fast chargers for electric vehicles) are carving out niches in technological areas.
In addition, there will be an array of well-established parts companies that were never part of the official government car plans. These include ARB Corporation, Harrop Engineering, Cyco Group, Albins Performance Transmissions and PWR Performance Products, all of which are producing world-ranked products focused on niche markets in off-road and high-performance parts.
It’s not clear how many of these companies, old and new, will be able to flourish in an industry when there are no car makers providing the stimulus for design, quality and efficiency.
But what is clear is that they will never replace the 40,000 full-time jobs and 60,000 full-time-equivalent jobs that will be lost when then last car factories close.
Here’s how some of these companies will be moving forward so that Australia can still claim to be an important player in the world motoring industry.
Motoring ahead
MtM: When you open a car door, there is a mechanism between the two hinges called a door check that prevents the door swinging all the way around and hitting the bodywork. MtM Automotive Components has excelled in making this specialised product for most of its 48 years. The company started exporting these in the 1990s, including to Cadillac in the US which it still supplies. It will lose about 25 per cent of its business when Holden and Toyota stop local operations in October but it has secured new orders in China to fill that gap and more. Crucially, while the final assembly will be done in China, the key component that contains MtM’s intellectual property will still be made in Oakleigh South in Melbourne, protecting the company’s expertise and competitive edge.
Unidrive: A leader in the manufacture and supply of drive shafts and propeller shafts to Australian car makers, Unidrive will lose around half of its business and half its 110-strong workforce when Holden and Toyota shut down.
However, over the past 20 years, Clayton-based Unidrive has developed specialised skills in order to service its major export contract, the supply of driveline support assemblies – where the driveshaft is enclosed in a torque tube – for Chevrolet’s high-profile Corvette sports car.
Its production of 35,000 to 40,000 units annually are too small for the global parts suppliers but just the sort of volume in which Australian suppliers specialise. Their product variants for the Corvette include full aluminium and combinations of aluminium and steel and aluminium and composite materials, all relatively high-value components that are still viable when exported.
Bosch Australia: Bosch came to Australia in 1955 with Volkswagen, but stayed on after VW left and became a crucial supplier of braking systems to the local industry.
Production of braking systems has since moved offshore due to dwindling volumes here but, like Ford and Holden, Bosch has retained its world-class design and engineering centre in Melbourne.
Australia is also Bosch’s global centre for the production of power diodes, a key component in vehicle alternators, and for trailer safety, developing systems that help control caravans, boat trailers and the like.
Carbon Revolution: This poster-boy for innovation sprang out of the Formula SAE-A competition for tertiary students run by the Society of Automotive Engineers Australasia. Students must design and build a single-seater racer within a strict set of rules, and in 2006 a group from Deakin University made their own carbon-fibre wheels as part of the project.
Several of the students went on to form Carbon Revolution and, 11 years later, the company is the world leader in lightweight composite wheels and has supply agreements for two top-end Ford sports cars.
Carbon-fibre products used to be labour-intensive because the fabric had to be manually laid up in the mould, but Carbon Revolution has mechanised and automated wheel production so it can move from selling a few high-priced wheels for exotic sports cars to high-volume production for everyday models.
Large-volume factories will likely be built next to car factories offshore, but small-volume wheels for planes and large trucks will be made in Australia.
Tritium: Brisbane’s Tritium is one of the new-wave companies making its own way in the world without car maker contracts. It manufactures the world’s lightest fast-charging system for electric cars and sells its products to operators of charging networks, including ChargePoint, the largest network in the US, as well as municipalities and building owners.
The company’s Veefil chargers weigh 160 kilograms, about a quarter the weight of competitors’ products, thanks to a unique liquid-cooled transformer that can operate in a wider range of ambient temperatures and needs much less maintenance. The liquid is cooled by a Formula One-spec radiator which is also made in Brisbane, by PWR Performance Products.
Tritium has just raised $5 million in capital to fund the commercialisation of its new, faster charger that will allow drivers to receive, in 10 minutes, a charge that is good for 150 kilometres. This triples the current standard of 50 kilometres worth of charge in 10 minutes.